Master of Science in Aerospace Engineering specialized in Aerodynamics & Computational Fluid Dynamics
Graduating 2027
Bachelor of Science in Aerospace Engineering with Honors
Graduated June 2025
I’m Michael West, an aerospace engineering student at California State University, Long Beach pursuing my M.S. Aerospace Engineering with hands-on experience in aerodynamic theory & design, composite manufacturing, and internship experience in product manufacturing engineering in the aerospace industry. My portfolio highlights my automotive FSAE experience where I used Ansys Fluent and analytical design work to optimize the car’s flow field and meet agreed-upon target metrics to create an effective aerodynamics package. Additionally, I have internship experience in aerospace manufacturing where I focused on CAD work and improving party quality through lean six sigma analysis and improvement. If you’re looking for a results-driven young engineer who can deliver consistent performance and dedication, feel free to take a look— I’d love to connect!
2024-2025 FSAE ANTEATER RACING
Process and simulation optimization and multi-element rear wing aerodynamic and structural design
Developed Guidelines for 2-D Ansys Fluent CFD Simulations
Purpose:
I created a comprehensive guide for the 2024-2025 school year to standardize 2D steady-state CFD simulations in Ansys Fluent for our FSAE team’s front and rear wing designs. This guide was necessary to ensure consistent, reliable simulation practices across different computers and users, as team members conduct simulations to inform design decisions and validate aerodynamic performance.
What I Did:
Defined Computational Domain and Boundary Conditions: Established guidelines for domain size and boundary placement to minimize boundary effects and ensure that results are physically meaningful and comparable.
Specified Mesh Criteria: Developed mesh quality standards, including target y+ values, mesh independence study protocols, and final mesh configuration, enabling accurate boundary layer and aerodynamic force prediction.
Set Solver Configuration and Convergence: Outlined solver setup and convergence criteria to ensure simulations are efficient yet robust, achieving reliable results.
Post-Processing and Data Management: Created protocols for recording and uploading simulation results, including lift, drag, and mesh quality metrics, to ensure all simulations could be used for informed comparisons.
Expertise Demonstrated:
CFD Methodology: Showed a thorough understanding of CFD principles, including boundary layer modeling, mesh independence studies, and turbulence model selection (k−ω SST selection justification), specifically tailored for aerodynamic applications.
Attention to Detail and Standardization: Demonstrated ability to create clear, detailed guidelines for consistent simulation practices, critical for multi-user environments and collaborative projects.
Technical Communication: Authored a structured, user-friendly guide, balancing technical depth with accessibility for team members of varying experience levels.
Project Management: Developed a systematic approach to ensure reliability and repeatability of CFD results, providing a foundation for future analysis and potential iterative improvements.
created physics-aware multielement airfoil plotting software
Purpose:
I used MATLAB to create a two or three element airfoil plotter with applicability to race car aerodynamics. I recognized a major bottleneck in my team’s workflow was our method of configuring different combinations of airfoils at different angle of attacks and slot gaps. The old method was to re-import the coordinates into SolidWorks and manually readjust each time we wanted to try a new configuration. My software has decreased the time required to visualize and generate a new airfoil configuration by as much as 90%.
What I Did:
Analysis tool creation: Created software that allows the user to input just the airfoil name from AirfoilTools (a database of over 1600 possible airfoils) of each airfoil, the desired angle of attack of the main element, and the desired slot gap. From that, the software uses calculations to automatically or manually align the second and third elements to the main element. The software also cleans the coordinates by closing the trailing edge if it is open and performing a smoothing algorithm for easier integration into meshing workflows.
Process optimization: The user no longer has to download the coordinate files for each airfoil, since the program automatically scrapes the coordinates and converts them from Lednicer to Selig format if necessary. The final output can be exported to a .dxf file for use in any number of CAD programs. The end user requires zero MATLAB knowledge because the entire process is automated and prompt-based.
Expertise Demonstrated:
MATLAB knowledge: The entire program is written in MATLAB and fully optimized. It also supports parallel computing through MATLAB’s toolkit.
Problem identification and solution: The project began when I identified a major weakness in our everyday workflow. Within two weeks, the team had a in-house analysis tool to streamline the process.
Fluid dynamics knowledge: The software implements equations derived from fluids first principles to automatically align the airfoils considering boundary layer effects and estimations. Alternatively, the user can manually input their desired angles of attacks.
2023-2024 FSAE ANTEATER RACING
Focused on creating the side pods of the 2023-24 car
DESIGN OF SIDE PODS (AERO-THERMAL VEHICLE PART)
Purpose:
I developed a detailed design binder containing my methodology and design to standardize side pod and ground effect design. This binder ensures cohesive, effective design practices across team members working on aerodynamic components, specifically focusing on engine cooling and aerodynamic efficiency. It was essential to establish guidelines that consider constraints, safety, and FSAE rules, enabling consistent and informed design decisions.
What I Did:
Defined Cooling and Aerodynamic Requirements: Established goals and constraints for the side pod design, including radiator airflow, boundary layer attachment, and turbulence minimization, to ensure optimal engine cooling while maintaining aerodynamic performance. Collaborated with other sub teams to reach the design goals.
Set Simulation and Verification Protocols: Outlined simulation methods using Ansys Fluent, including boundary condition settings, mesh generation with Fluent Meshing, and turbulence modeling (realizable k-ε model), to accurately capture flow behavior and velocity deficits caused by the rolling tire wake.
Implemented Flow Control Design Features: Introduced design strategies such as gills, chimneys, and expanded cross-sectional areas to manage airflow through the radiator, balancing improved cooling with minimal drag.
Developed Real-Life Testing Plan: Created a verification plan involving flow visualization through tufts and computational simulations for assessing design effectiveness post-installation, with specific metrics for tuning and further adjustments as needed.
Expertise Demonstrated:
CFD Application in Aerodynamics: Demonstrated a solid understanding of airflow management and boundary layer dynamics within complex geometries, particularly in settings requiring minimal turbulence and consistent velocity fields for cooling efficiency.
Technical and Regulatory Compliance: Ensured the side pod design adhered to FSAE bodywork and aerodynamic rules, including bounding box constraints, through systematic consideration of rule requirements.
Problem-Solving and Analytical Modeling: Employed a velocity deficit model to approximate flow behavior in the side pod inlet, adapting wind turbine models to automotive aerodynamics for addressing limited computational resources and time constraints.
Collaboration and Documentation: Produced a structured, comprehensive design binder, enhancing communication among team members, particularly between aerodynamics and powertrain teams, and setting a foundation for future design improvements.
2022-2023 FSAE ANTEATER RACING
Apprenticed with the Powertrain Sub-team, working on fabrication and CAD management
MUFFLER MOUNTING AND HEAT SHIELD
Purpose:
My first year on FSAE focused on fabrication and supporting the team’s CAD documentation efforts.
What I Did:
Muffler: I worked on designing and fabricating both the mounting and heat shielding of the muffler to align with FSAE rules and regulations.
CAD: I also worked on the creation of 2-D drawings of various parts on the car for documentation and manufacturing.
Expertise Demonstrated:
Fabrication: Used power tools and precision hand measurement devices to build the mounts and heat shield while staying true to the CAD within specified tolerances
SolidWorks: Used SolidWorks extensively in the iterative design process
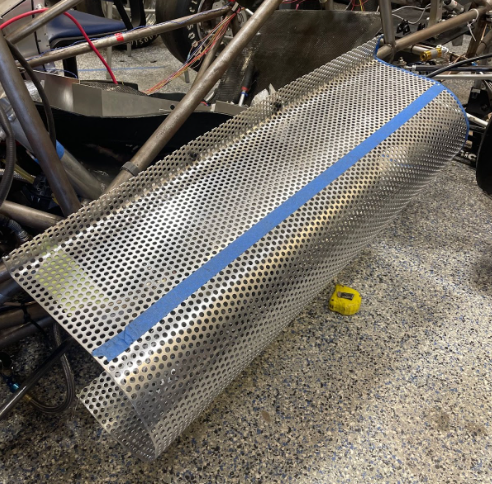
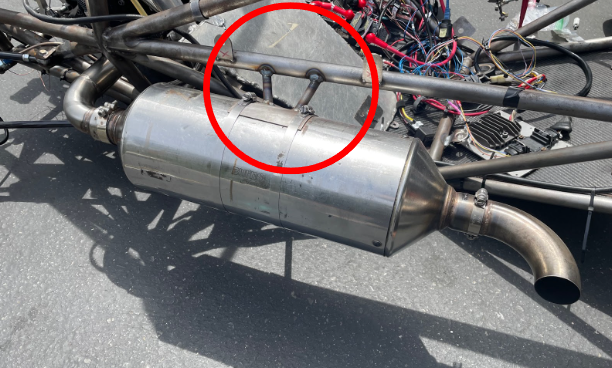
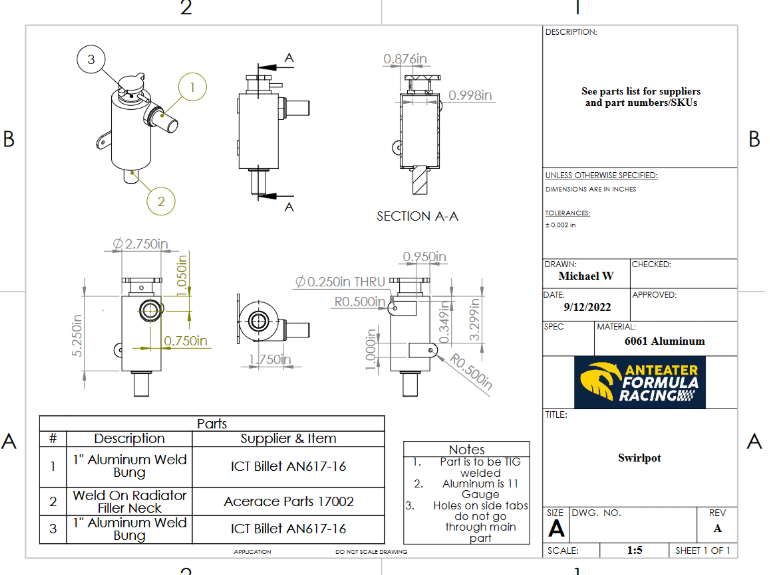
FRC Robotics
Design and fabricated gearboxes and frame chassis of a large scale robot.
drivetrain development
Purpose:
Design, prototype, and fabricate a chassis and drive system within the constraints of the competition rules and tight timeline.
What I Did:
Design: Design a custom chassis out of 2″x1″ aluminum stock with in-house machined aluminum gussets. Accommodate all robot systems such as arms, elevators, and supports. Engineered custom gear trains based on speed and torque requirements.
Fabrication: Fabricate chassis system from scratch. Ensure survivability in high-contact and high-impact environment.
Expertise Demonstrated:
Fabrication: Used power tools, precision hand tools, CNC mills, and laser cutters to fabricate individual components. Integrate all components, ensuring squared chassis and aligned gear train with chain.
SolidWorks: Used SolidWorks extensively in the iterative design process
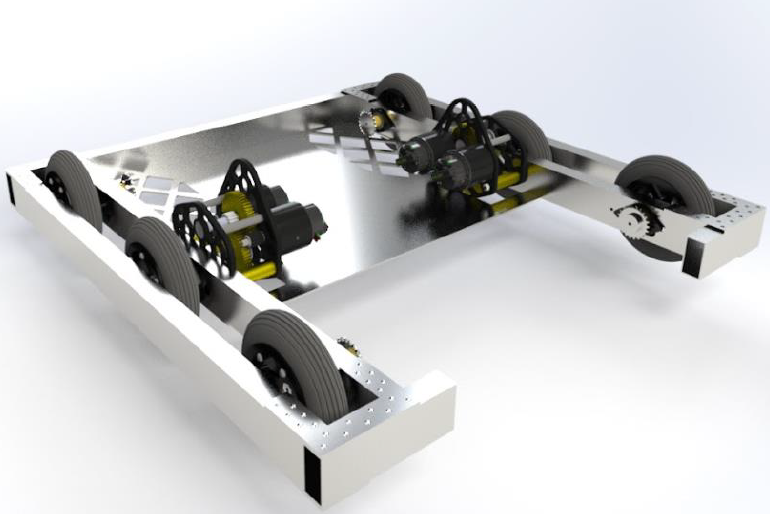
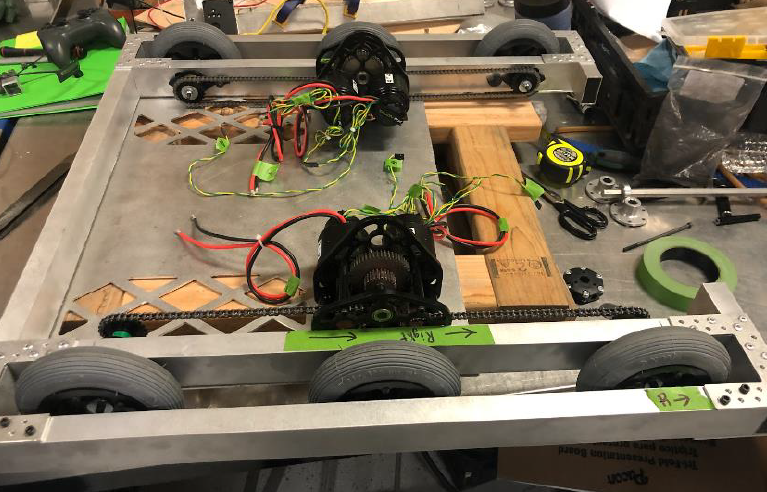
SELECTED PERSONAL AND ACADEMIC PROJECTS
Projects showing skills in aircraft performance analysis, Python & MATLAB scripting, and application of engineering skills to hands-on projects
RESEARCH PAPER: CFD and Analytical Modeling of Contrail Particle Size Reduction via Fluorosurfactant
PRELIMINARY DESIGN AND SIZING OF A COMMERCIAL SUBSONIC TRANSPORT AIRCRAFT
Applied Engineering in Classic Car Restoration: Structural, Mechanical, and ELECTRICAL System OverhauL
Purpose:
The goal was to “resto-mod” a classic 1976 Jaguar XJ6-C by integrating modern powertrain technology and restoring all key systems, from the engine and electrical wiring to bodywork and suspension. This project required engineering solutions to blend vintage automotive design with modern performance standards, showcasing a real-world application of engineering principles.
What I Did:
Powertrain transplant: Engineered a novel custom transplant of a modern Jaguar engine into a classic car shell, adapting all supported systems to fit the new powertrain
Electrical overhaul: Overhauled the electrical systems by manually simplifying a complex 14 module setup to work with the classic design and system. Engineered custom wiring harness solutions to blend the old with the new.
Restoration: Conducted a full vehicle restoration, including bodywork (sanding, painting), interior updates, and a suspension rebuild to ensure structural and aesthetic quality
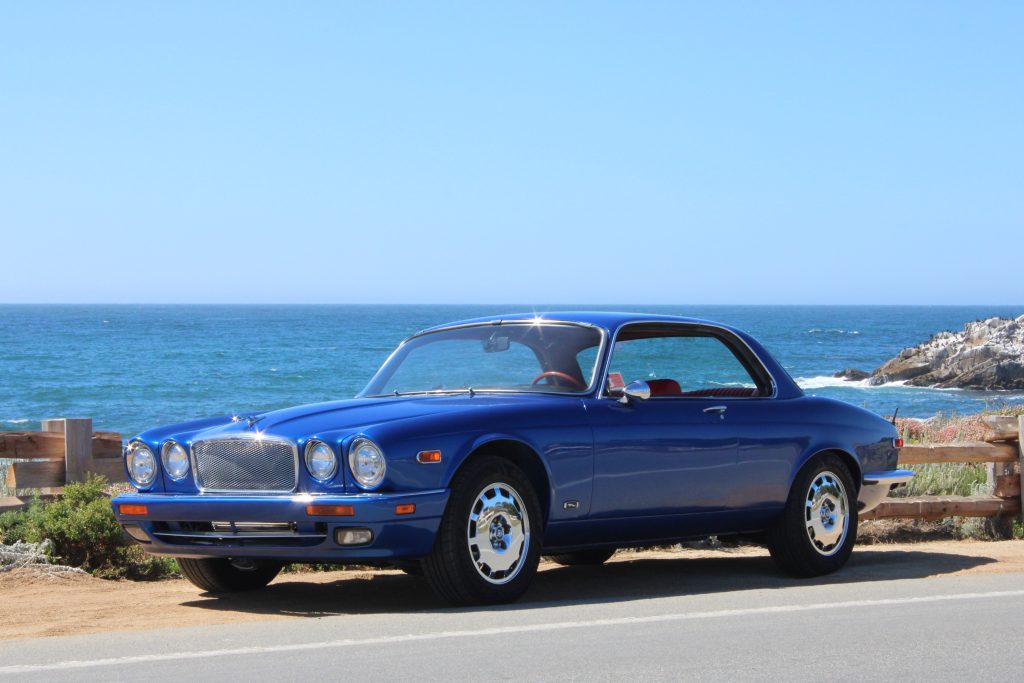
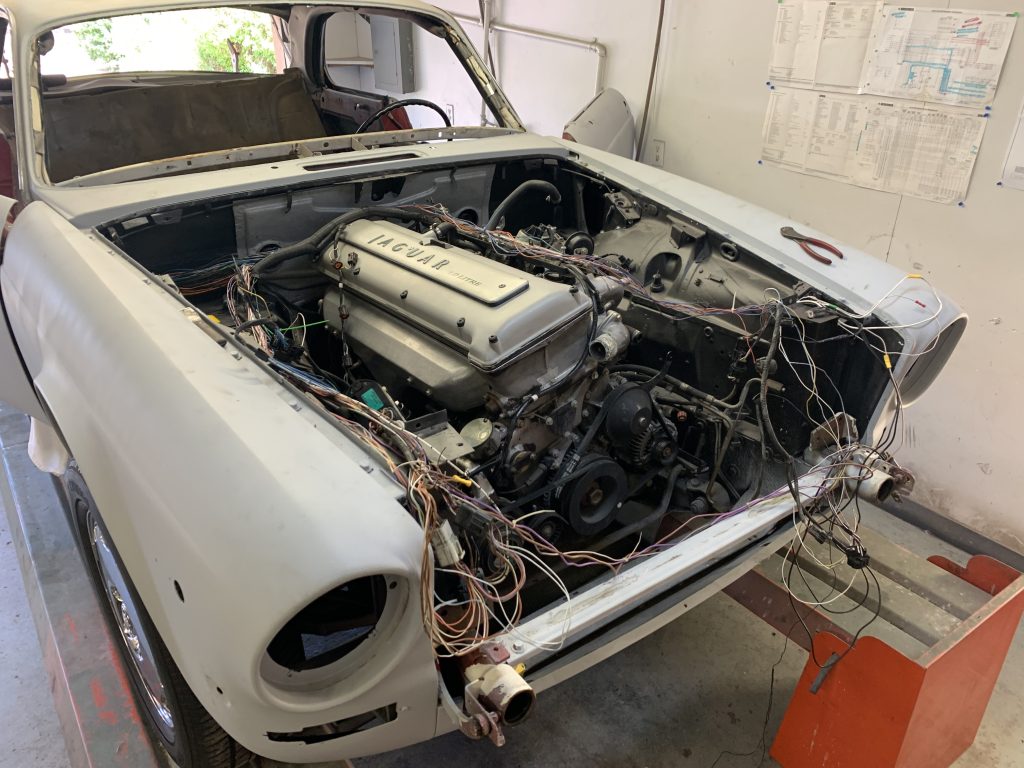
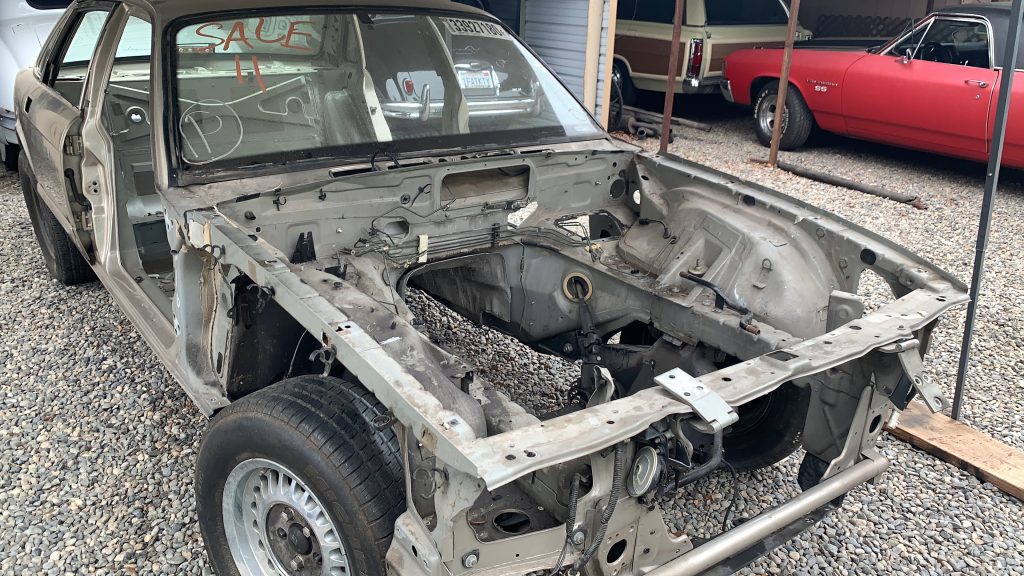

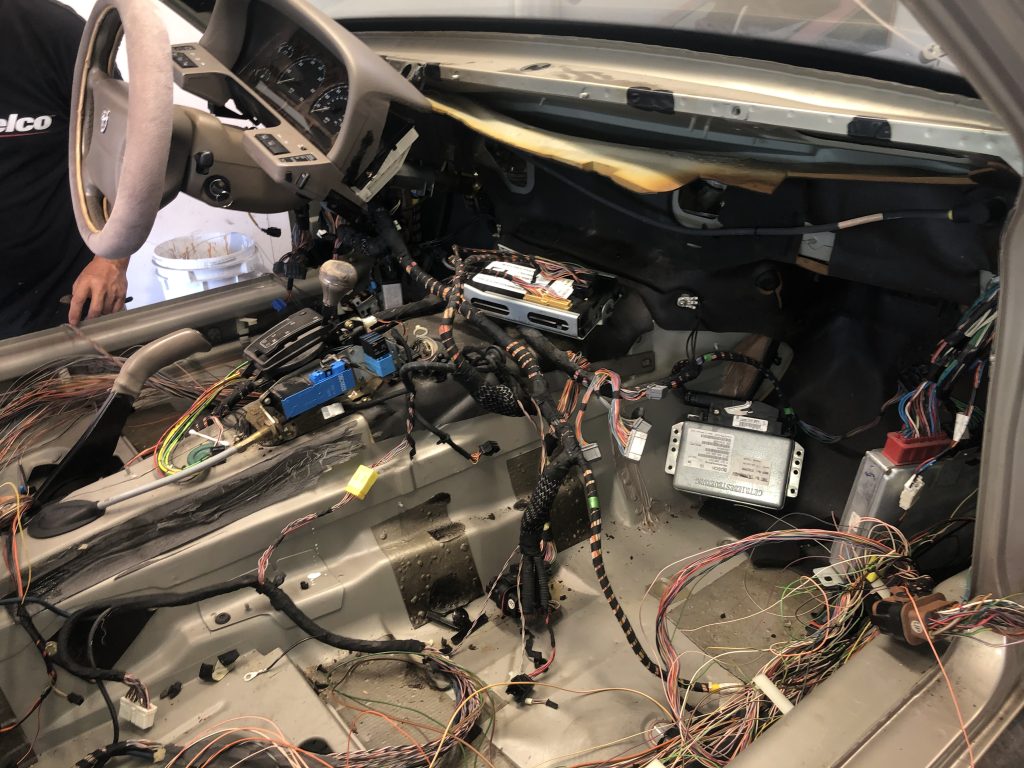
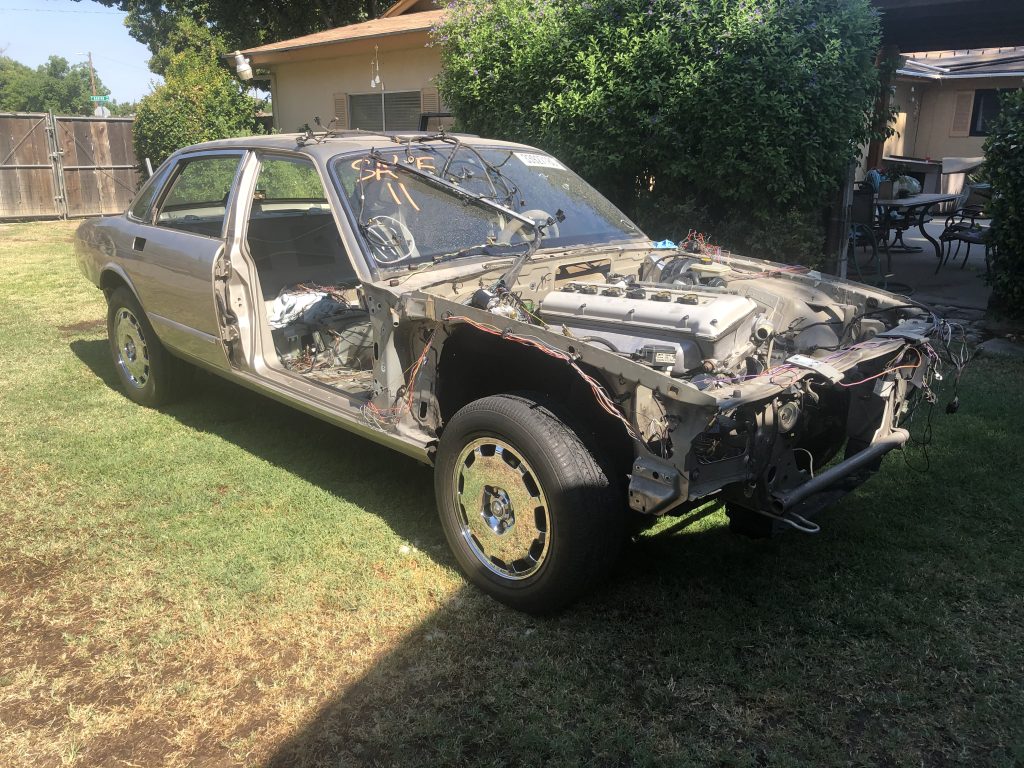
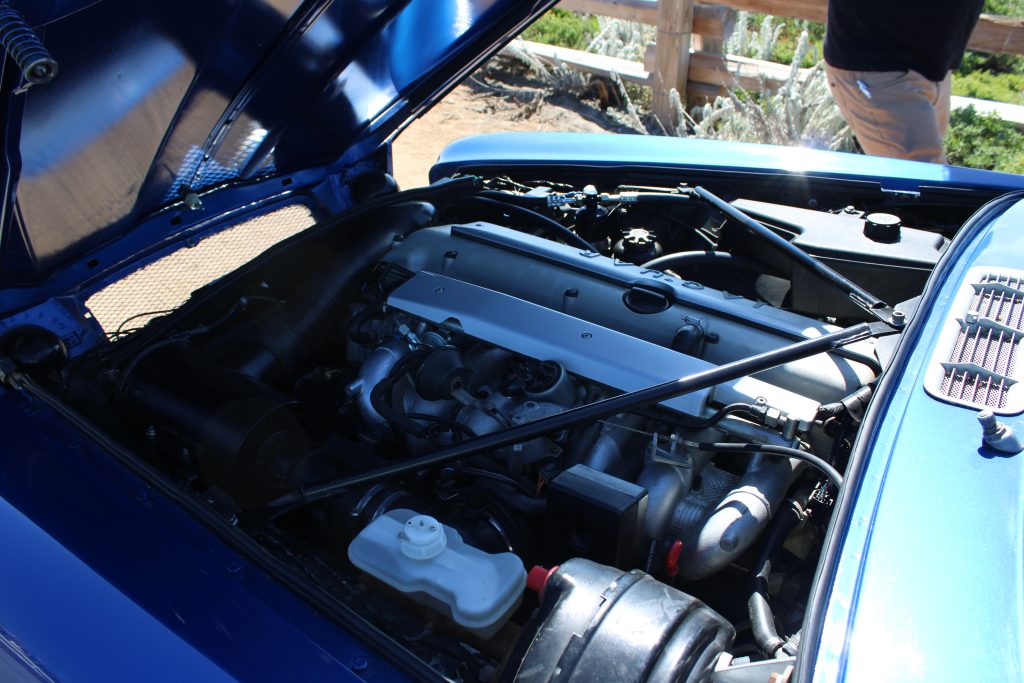
Expertise Demonstrated:
Systems Integration: Adapting modern and legacy automotive technologies, ensuring compatibility and functionality as well as compliance with various California statutes
Electrical Systems Knowledge: Simplifying and implementing electrical systems from complex, multi-computer configurations to streamlined, manageable circuits. Required reading and comprehension of an over 100 page whole-vehicle electrical schematic.
Mechanical and Structural Insight: Engaging with automotive design through metal fabrication, suspension work, and internal combustion engine mechanics.
Problem Solving and Project Management: Addressing unforeseen challenges in restoring a unique, aged vehicle and coordinating tasks to achieve comprehensive restoration.
The completed project has gone on to win awards and accolades at prestigious car events across California. It has also been featured in an article by Hemmings Magazine.